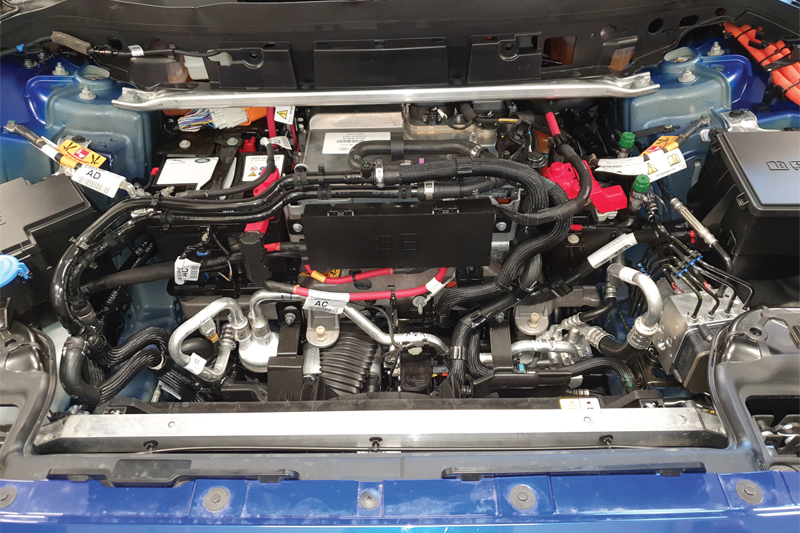
Steve Carter explains how the battery thermal management system may hold the key to unlocking the potential of electric vehicle batteries, and therefore why aftermarket businesses need to stay clued up on this area of new technology.
In recent times, it seems like there isn’t a week that goes by without a vehicle manufacturer announcing a new range of electric vehicles, with consumers wanting to know what’s different.
There are multiple factors that affect the range of an electric vehicle (EV) that are not limited to the battery alone. Most vehicle manufacturers work on the assumption that 300 miles on a single charge is sufficient for most consumers.
However, many now want to see quicker charging speeds that will require a shift away the battery composition of NMC 622 to the NMC 811 formula. Whilst independent garages and factors will not be concerned with the specifics of this battery chemistry, it is essential that they have a sound understanding of the battery thermal management system in order to extrapolate the potential offered by these new batteries, so that they can provide maintenance and support for electric vehicle owners.
The performance of lithium ion battery cells is greatly impacted by their temperature. Lithium ion battery cells suffer from the ‘Goldilocks effect’; they do not perform well when too cold or too hot, which can lead to permanent and extreme damage of the cells or accelerated degradation. So, whilst these batteries need cooling to prevent damage, they will also need heating at lower temperatures to prevent damage during fast charging when the cells are too cold. This is because the internal resistance of the cells rises when they are cold. Most lithium battery cells cannot be fast charged when they are less than 5°C and cannot be charged at all when they are below 0°C. Lithium cells also begin to degrade quickly when their temperature is above 40°C.
The real new nuance of battery thermal management is to achieve the required temperature parameters whilst using as little energy as possible. Whilst this poses a challenge, some of the latest EVs have been able to overcome this with varying degrees of success. The Jaguar I-Pace has a triple heat scavenging system that utilises the air conditioning system as a heat pump.
It consists of three refrigerated heat exchangers, three circulation electric pumps and a split cooling system. Firstly, the system cools the battery because it has the lowest working range (c.20.C), meaning that the first radiator/heat exchanger at the front of the vehicle is for the battery only.
The next is the radiator/heat exchanger, which is for the front and rear electric motors, and the front and rear power electronics.
The radiators/heat exchangers for both the front and rear electric motors, and the front and rear power electronics, have their own independent circulation pumps.
However, the coolant will be collectively cooled in the front exchanger positioned behind the battery heat exchanger. The last heat exchanger – with the highest working temperature – is the air conditioning condenser; when required, this whole system can be assisted with an 850W fan.
Thermal management strategy for the I-Pace
If the ambient air is less than 20°C, allow for HV battery cooling in drive mode. Active vanes will open and close as needed, and if an uneven cell temperature is detected, the solenoid valve will send coolant to the HV pack, bypassing the heat exchanger to ensure active cooling.
As cell or ambient temperature rises above 20°C, the active vanes open, and a cooling pump circulates coolant through a front heat exchanger. If this is insufficient, a proportion valve will bypass the coolant through a refrigerant chiller.
When rapid charging at a low cell temperature, a heat pump system is used to pre-condition (heat) the HV battery to the required range. This type of heating is much more efficient than a PTC heater.
To heat the passenger compartments, a heat pump becomes active. Heat is recovered from the drive unit and the power electronics cooling system, even with efficiencies of above 95%, and usable heat can still be recovered by the third refrigerated heat exchanger.
This is why the cooling/heating system is referred to as a triple heat scavenging system.
The vehicle in question may not require some of the servicing that we have become accustomed to, but the air conditioning and cooling system now work as one, and can now play an important part throughout the entire vehicle.
Only with the approved training and appropriate knowledge can these systems be serviced and repaired safely and professionally.