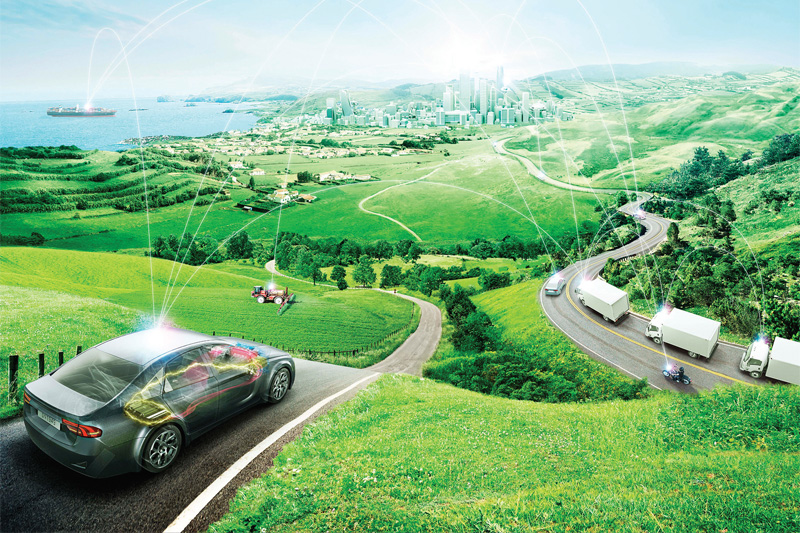
Denso Aftermarket’s Assistant Manager, Aftermarket Network UK & IE, Mike Sadler, explains how the company has adapted to the needs of a more sustainable aftermarket.
The increasing popularity of hybrid and electric vehicles has required parts manufacturers to evolve existing technologies and develop entirely new ones in order to offer the most innovative, efficient and reliable parts for these engine types. As such, Denso Aftermarket claims to have made revolutionary progress with rotating electric machines, as well as compressors and sensors.
Within hours of the UK Government announcing its intention to ban new petrol and diesel car sales by 2035, online searches for electric cars surged by 162% above average levels, according to Auto Trader. This renewed consumer interest corresponded with a continued increase in sales of hybrid and electric vehicles in the UK.
Electric vehicle sales rose sharply in February, according to Society of Motor Manufacturers and Traders figures, increasing from 731 to 2,508 in 2019, a rise of 243.1%. This translates to 3.2% of the new car market.
Hybrid sales also climbed, despite the government’s choice to blacklist the vehicles in 2035, with almost one-in-five cars (17.5%) sold being either fully electric or hybrid, running on technology that includes both an engine and a battery.
As more initiatives are put in place to increase the use of sustainable mobility solutions, the need for automotive manufacturers to be forward-thinking has never been greater.
Denso Aftermarket claims to be dedicated to technological development and recognises itself as having been at the forefront of innovations since the electrification of vehicles began. Its increasingly varied catalogue of part numbers and a host of technologies are testament to the company’s progressive approach.
Mike Sadler, Denso Aftermarket’s Assistant Manager, Aftermarket Network, UK & IE, commented, “Since we introduced an e-compressor with an integrated inverter for hybrid cars in 2005, there have been several Denso Aftermarket breakthroughs which have contributed to the rapid increase of electrified parts. An integrated hybrid control computer, battery monitoring unit, DC-DC converter, superior battery cooling system and high-output power control unit (PCU) are all evidence of our innovative stance on electrification.
“As well as pioneering the increased handover from traditionally-fuelled engines to hybrid, we regard ourselves as responsible for the continued improvement and evolution of parts for hybridised powertrains.”
The evolution of rotating parts
As a replacement for conventional starters and alternators, Denso Aftermarket has crafted a motor-generator (MG) stator for use in hybrid vehicles.
The MG component performs several functions, including starting and assisting the engine, generating electric power, and driving the axles.
Mike added, “Several significant developments have already been made with this range of specialised products. Drawing on the experience used to create the segment conductor (SC) alternator, we developed a completely new MG stator for the Prius that is smaller and lighter by more than 20% compared to the previous generation, helping the vehicle to achieve a fuel economy of 40km/L.”
Creating the e-compressor
Denso Aftermarket claims to be responsible for the world’s first mass-produced electric compressor with an integrated inverter and motor.
On the company’s compressors, Mike noted: “Whilst conventional compressors are driven by the engine, making them unsuitable for use in hybrid vehicles, our e-compressor is driven by an internal motor. This not only makes it applicable to hybrid engines, but it also improves fuel efficiency as well.
“In the case of a hybrid powertrain, it is possible to run air conditioning functions, both when the engine is idling and switched off, thanks to the power provided by the internal motor of the e-compressor. This represents a significant advantage over traditionally fuelled vehicles, as it maintains a comfortable cabin environment whilst saving on fuel wastage.”
New sensor technology for electrical components
In hybrid vehicles, the petrol engine part of the powertrain is monitored by standard engine management system (EMS) sensors.
However, there is also the addition of several other sensors specific to high voltage (HV) electrified components. The development of these types of sensors is a direct result of the electrification trend and the rise of alternatively fuelled vehicles.
Sensors specific to hybrid/electric vehicles include:
- Battery current sensors: Which detect current flow and monitor the state of the main HV battery charge (SOC)
- Rotational angle sensors (Resolver): An indispensable sensor for optimal MG control
- System main relay (SMR): A high voltage relay for the safety and protection of the hybrid system’s main power supply – the HV battery
Mike concluded, “It is clear that the technological advancements made by Denso Aftermarket have helped to shape the current face of hybrid vehicles.
“As the move toward electrification continues, our pioneering parts will evolve into new spheres of technology and sustainability.”