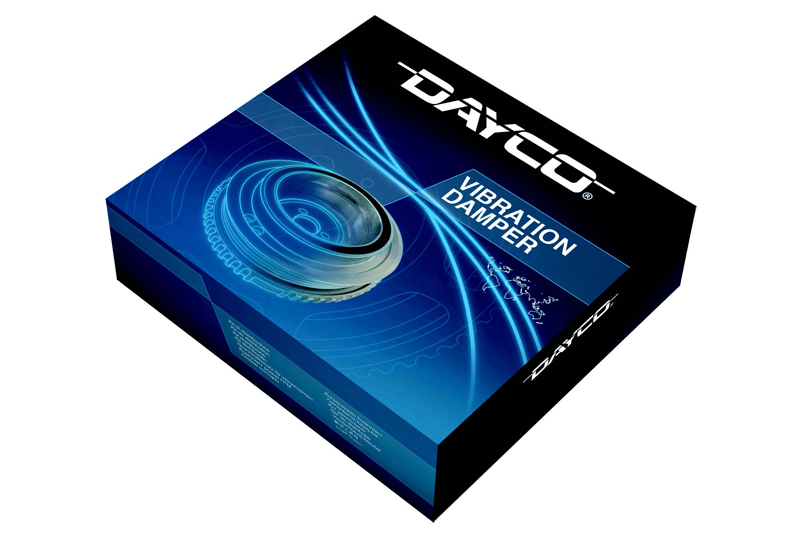
Dayco is a producer of original equipment (OE) torsional vibration dampers; the same product line is available to the aftermarket. Here, the company explores the ins and outs of this important product category.
Modern powerplants are highly engineered to deliver the optimum combination of power and torque, alongside fuel efficiency and minimal exhaust emissions. This objective often comes at the cost of high levels of engine vibration, which is generally intensified by the significant pressures present in the engine’s combustion chambers, an occurrence especially prevalent with diesel units.
This vibration is transmitted through the crankshaft and therefore has a significant impact on the engine’s power transmission drive systems. To reduce this problem, Dayco engineers have developed the damper pulley, or DPV.
Generally installed directly to the crankshaft, the damper reduces the circular vibrations that cause the primary problem, decreasing wear on many of the engine’s components. Naturally, the front end auxiliary drive (FEAD) system is a principal beneficiary, which increases the durability of the entire powerplant and improves comfort for the vehicle’s occupants.
There are three types of damper that, depending on the application, are generally installed: the simple, double and decoupler.
Rather than being connected straight to the crankshaft, the simple damper is integrated within the FEAD system, as this provides sufficient vibration reduction for applications with standard NVH (noise, vibration and harshness) requirements.
The double damper encompasses two rubber elements within its metal parts, which are designed to absorb vibration at different frequencies, and is for use in applications that generate high power and increased vibration, such as modern diesel engines.
Although the decoupler damper still incorporates a rubber ring, the damping function is carried out through metal springs, as opposed to solely relying on its rubber element. It is used on the latest generation engines with greater power and enables the FEAD system to cope with high mileage and adverse conditions, particularly for applications that feature a BSG (belt start generator) function.
Damper replacement
Naturally, as with every wearing part, over the course of time and as the vehicle’s mileage increases, problems can occur and the damper can lose its efficiency or sometimes even break, which itself obviously increases the risk of failure in other parts of the engine’s drive systems.
To avoid these problems, dampers should be checked for signs of wear, such as abnormal noises, unpleasant vibrations or even steering oscillations, at every 40,000m interval or when replacing the auxiliary belt. However, as a matter of course and irrespective of the signs, Dayco suggests they are changed every time the timing belt is renewed.
Technicians must be aware, however, that in order to check the damper correctly, it needs to be removed from the engine because the back, as well as the front, needs to be examined to fully assess its condition. In addition, whether it needs to be replaced or not, the bolts must be changed, as they are designed to stretch on initial fitment and will no longer meet their design tolerances if reused.
Aftermarket solutions
In common with all the products that Dayco manufactures, its DPVs are produced in the same facilities, to identical standards, so whether the damper is destined for OE or aftermarket supply, it is of the same quality, which provides peace-of-mind to both the workshop and its customer.
For maximum convenience and to ensure the highest standards are maintained during its installation, each damper in the 160 plus-strong Dayco range that technically also requires its bolts to be replaced, comes complete with the correct specification bolts. This assurance and the 95% vehicle parc coverage the programme provides, makes Dayco DPVs the ultimate choice for the discerning aftermarket professional.