Supporting the purchasing of remanufactured engines
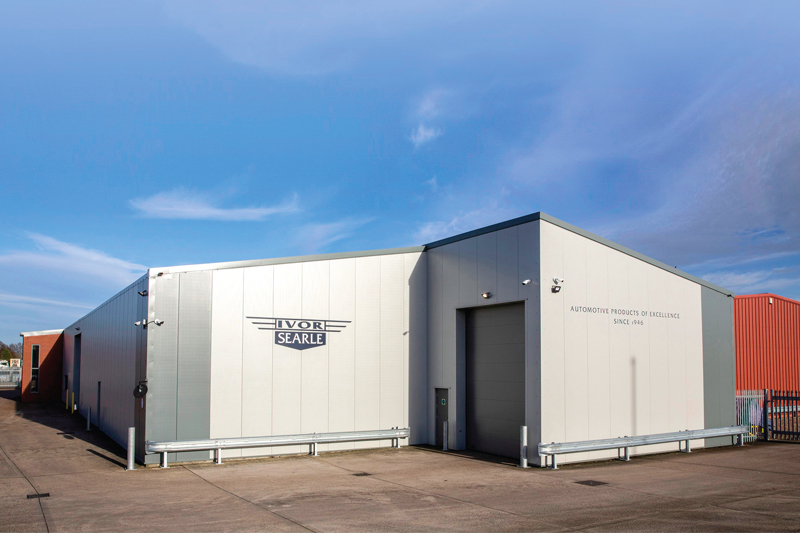
Remanufactured engines are arguably one of the highest value products that you sell to workshops. Typically a distress purchase due to powertrain failure, it is important that workshops buying major units are provided with accurate product information, effective sales support and robust warranty protection, according to Ivor Searle.
This, according to the engine remanufacturer, enables you to offer workshops the reassurance that sourcing a quality remanufactured engine is the right choice and also serves the best interests of the end-user.
Price and sustainability pivotal points
Price is a “key advantage” for workshops purchasing remanufactured engines, with “quality replacement” major units costing around 40% less than a brand new OEM product. This helps to minimise the cost for the customer and also provides the workshop with a competitive edge when it comes to securing repair work.
Furthermore, Ivor Searle believes remanufactured units also offer a more sustainable solution, as considerably less energy and materials are used in the remanufacturing process; for example, it claimed that its remanufactured engines conserve approximately 55 kilos in core metal, and around 85% of the engine’s original components are returned to OEM specification.
Lowdown on Ivor Searle
Established in 1946, Ivor Searle serves over 1,500 factor outlets throughout the UK and overseas. Producing around 8,000 units each year, the family owned and managed company offers an all-makes range of car and LCV petrol and diesel engines, as well as cylinder heads, gearboxes and turbochargers that cover over 90% of the UK vehicle parc. The range is constantly expanded to ensure it meets the needs of the market.
Support is provided by Ivor Searle’s experienced sales and customer service team, as well as a full e-commerce website which enables quotes to be produced “quickly and easily” as well as orders to be placed online. Featuring a vehicle registration number look-up facility, in addition to searching by vehicle make, model or engine code, the website also provides technical details and major unit installation instructions.
For peace of mind, all Ivor Searle engines, cylinder heads and gearboxes are covered by a transferable 12-month unlimited mileage parts and labour warranty, while a two-year warranty covers all turbochargers. All products are also supplied with pre-installation guidelines for the workshop and model-specific instructions where required.
Ivor Searle holds “comprehensive stocks” to ensure excellent customer service and minimum vehicle downtime. It provides free next-day UK mainland delivery on stock items ordered before 3.30pm. The remanufacturer also aims to make the exchange process for major units simple and provides purpose-designed cradles for engine delivery and return of the exchange unit to ensure the process is safe and straightforward for the workshop.
On the “rare occasion” that an enquiry cannot be fulfilled with a stock or production engine, Ivor Searle also offers a customer own unit remanufacturing service. This provides you with the opportunity to supply workshops with a solution for virtually any car or LCV engine application, as David Eszenyi, Ivor Searle’s commercial director, explains:
“The customer own unit service involves collection of the original failed unit from a factor’s workshop customer and returning it to our factory in Soham, Cambridgeshire, where it undergoes exactly the same intensive inspection, cleaning and remanufacturing processes as our volume products.
“Produced in accordance with BSI AU 257:2002, the British Standard Automobile Series Code of Practice that applies to the remanufacturing of internal combustion engines, these processes include the detailed inspection and checking of components against manufacturer tolerances.
“In addition, key parts – including pistons and ring sets, big and small end bearings and bushes, as well as gaskets, seals, timing chains and drive belts – are all renewed, while items, such as tensioners and dampers, are inspected and replaced if necessary to ensure the original specification of the engine is achieved with full reliability.
“Providing parts are available, customer own unit engines have a 10 to 15-day turnaround time from receipt of the failed unit and are covered with the same 12- month unlimited mileage warranty as our production range of engines. Customerowned unit remanufacturing service expertise includes the very latest engines, which are not currently available, and rare units, such as the BMW V8 found in M5 models, alongside engines for factors serving the classic car market, such as the Jaguar V12 for the E-Type.”