How the next generation can bridge the skills gap
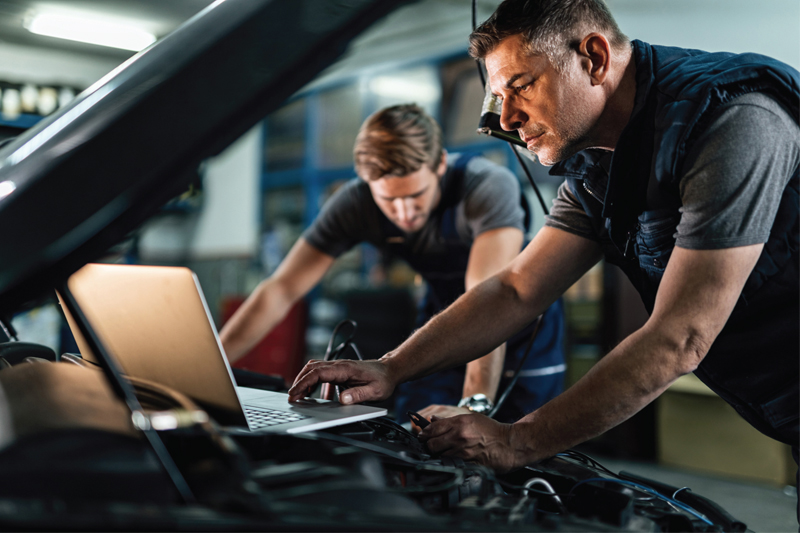
The skills gap and attracting the next generation of automotive talent are intrinsically linked. We address the issues, potential reasons behind them, but also share some of the ideas, solutions and real-world stories to narrow the window, inspire and protect our sector.
In 2022, the Institute of the Motor Industry (IMI) predicted a 160,000 shortfall of workers in the UK automotive sector in the next decade, forecasting a 2% decrease in the number of jobs available in the sector by 2031 – blaming an ageing population, decreased immigration and the ‘green agenda’ for creating a major skills challenge.
Commenting on its Automotive Sector Employment report at the time, IMI CEO, Steve Nash, said: “An aging population is a significant contributor to the dilemma. Many of our older workers are set to retire over the coming years and fewer younger workers are joining the labour force. Without doubt, more needs to be done to attract young blood into the UK’s automotive sector.”
Encouragingly, however, the IMI announced that the number of automotive apprenticeship starts in England, in the first three months (August to October) for academic year 2023/24, was 9% higher than the same period last year; in fact, it was the highest first-quarter performance since the academic year 2019/20.
IMI Research Manager, Emma Carrigy, said: “This uplift indicates a renewed interest in both the automotive sector generally and apprenticeships as an entry route, both of which are critical to build the talent pipeline for the future.
“Our new analysis suggests automotive is gaining a broader appeal, potentially fuelled by the advanced technologies that are becoming more commonplace, such as ADAS and electric vehicles.
“And what is particularly interesting is that there has been a pronounced uplift in intermediate-level apprenticeships, which may reflect a growing demand for foundational skills and entry-level qualifications, possibly serving as a gateway to more advanced training or responding to current job market needs.”
Despite the IMI’s encouraging figures, there is work to be done. The industry as a whole is working hard in improving matters: in an era marked by rapid advancements, Alliance Automotive Group Training Manager, Scott Simpson, recognises the pivotal role of education in bridging the skills gap within the industry:
“The rapid advance of vehicle technology has changed the landscape for the modern automotive technician. Showing no sign of slowing, future developments risk the industry skills gap widening still further.
“Each new and emerging technology delivers a fresh challenge for technicians, who have already seen their skills requirement widen. As such, the value and importance of training to narrow the skills gap cannot be understated.
“Working with high voltage vehicle systems can carry personal risk, as well as bringing new technical challenges. Workshop Pro Training offers EV courses from 25 quality training providers across the UK and Ireland at levels one to four. Their popularity demonstrates both the demand and value technicians receive from this training.
“To remain effective in this changing world, there are training needs in many more areas, ADAS systems, high voltage air conditioning systems, business skills and compliance training, OEM diagnostics and hydrogen vehicle systems to name but a few…”
The Lucas Oil Academy continues to gain momentum, with Leicester College and Furness College hosting rounds of technical training. These sessions aim to explain the evolving role of additives and lubricants in modern vehicle maintenance.
At Leicester College, the LOA team met level one, two and three students, while, at Furness, there was a mix of students from both the engineering and automotive faculties. The brief in each case was to provide an overview of the commercial side of the industry, to help students develop a greater understanding of additive technologies, which, according to Lucas Oil, are increasingly seen as advanced engineering solutions.
These sessions always include an overview of potential career opportunities, with the LOA collaborating with Mike Smallbone of Aftermarket Business Solutions. Mike, bringing his wide-ranging CV to the fore, discusses the pathways and potential roles within workshops, motor factors, retailers and other distributors.
The importance of skills and training within our industry cannot be overstated, according to Autoelectro’s Harnek Bhogal: “At the heart of our success lies in the expertise of our engineers, many of whom boast decades of experience in remanufacturing starter motors and alternators.
“Their wealth of knowledge isn’t merely confined to replicating existing products; it’s fuelled by a relentless pursuit of improvement and innovation. This technical acumen isn’t exclusive to the production floor; it permeates throughout our entire organisation, including our sales team.
“Situated on-site alongside our production facility, our sales team undergoes comprehensive training to ensure they possess an in-depth understanding of our products and their components. This knowledge is invaluable, particularly when addressing customer enquiries pertaining to specific vehicle applications or nuanced alternator configurations, as it means we offer our customers the best service possible.”
Last year saw a “back to basics” approach from many businesses, as the industry “wrestles” with both upskilling for emerging technologies and immediate technician shortages, according to Delphi.
UK and Nordics Technical Services Manager, Luke Garratt, said: “We had a rise in EV training demand, as we had anticipated; however, we saw a much more dramatic increase in people going back to ‘grassroots’ training.”
Demand for training on topics like wheels and tyres, braking systems, steering and suspension and four-wheel alignment surged. Delphi believes this is caused by difficulties experienced by many businesses in recruiting skilled technicians.
Luke continued: “For many garages now, that really experienced member of the team in the workshop, that would help everyone and offer their advice or opinion, just isn’t there anymore. This means the only option is to get people on board and then train them on the basics.”
Autosupplies Group Managing Director, David Clarke, said: “Training and recruitment are the two biggest issues facing our trade. Training staff helps to improve customer service, giving customers the correct information and sending the correct parts first time.
“We need a reframe of the parts industry; within Autosupplies there are numerous roles spanning telesales, customer services, sales, warehousing and logistics to name but a few. The motor trade can offer a very varied career for anyone, and it needs to be encouraged.
“All employees have their own training programmes to ensure development, and those employees that need training are focused on and given the support they need.
“With these changing requirements and evolving customer base, our future is all about our people, the team. We have to ensure employees are fully trained and our recruitment process is the best it can be.
“We conduct regular staff training sessions with suppliers, internally onsite and externally with suppliers.”