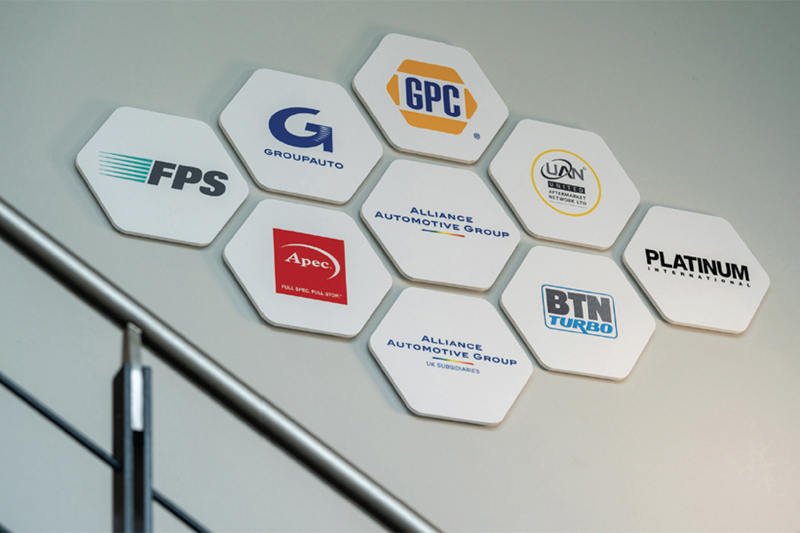
Following the announcement that Alliance Automotive Group (AAG), in partnership with Panattoni, will build a new distribution centre in Rotherham, we contacted AAG and asked to speak with its UK Group Logistics Director, Neil Warren – here’s how the conversation went:
Q. What does news of a new FPS distribution centre say about the direction of AAG and, specifically, FPS?
A. “The recent news regarding the new national distribution centre being built in the UK, opening early 2025, shows a real and sustained commitment from AAG to the development of the business infrastructure here in the UK.
“It will help support our customers across the UK aftermarket. Although we have already increased capacity of FPS, this is still the single biggest investment we’ve made since the acquisition. This investment will give the business the ability to offer an even wider range of solutions, underpinned with a high level of availability and ensure we are an ‘easy to do business with’ supplier for the market.”
Q. In the release announcing the new distribution centre, you mentioned “best-in-class logistics” and “advanced technologies” – are you able to expand on these statements?
A. “A number of the latest market-leading technologies will be utilised in the new operation. This will help ensure that each order taken and processed is done efficiently, quickly and with a level of accuracy that will be unsurpassed. Our existing operations team will be at the heart of the new distribution centre, bringing a level of commitment and passion that we continue to be proud of.”
Q. In the same release, you mentioned “an even wider product offering” – again, are you able to develop this and reveal what customers can look forward to in the next couple of years?
A. “We believe we have the best product offering in the market today. NAPA, an iconic global brand, has already become our biggest selling brand, closely followed by Apec, thanks to the support of our customers.
“In addition, our expansion with supplier brands, like Bosch, Gates, LuK, KYB and ZF TRW, to name a few, continue to be a crucial part of providing customers with the product solutions they need. Added to that is our rapid expansion into EV products and services, including the launch of our EV garage module, NexDrive, to ensure we’re able to support our customers well into the future.”
Q. Six years since the acquisition of FPS, along with Apec and BTN – how would you describe the impact this has had on AAG and, ultimately, the industry?
A. “FPS, Apec and BTN were all good businesses when we acquired them, but the backing and resources of AAG meant we were able to invest in capacity and growth, improving our customer offering along the way. In that sense, the impact on both AAG and the wider industry has been hugely positive.”
Q. In 2022, AAG signed an agreement to acquire Knoll GmbH, as well as add several motor factors to its portfolio – can we expect a similar pace and strategy this year?
A. “We’re part of the largest aftermarket distribution company in the world, so expansion and acquisitions remain a key part of our strategy. You mention Knoll in Germany, but we also acquired Lausan in Spain and Soulima in Portugal, along with several factors in France, Netherlands and Belgium. From a UK perspective, we made nine acquisitions in UK and Ireland in 2022, and would expect that rhythm to continue over the coming years.”
Q. With just over 5,500 staff, AAG serves over 30,000 technicians around the UK and Ireland, from more than 240 owned factor outlets, plus another 560 affiliated to the group – big numbers! – how much of a challenge, logistically, is it?
A. “It’s a huge, exciting challenge, but one we relish! We’re fortunate to have been able to adapt our logistics infrastructure to meet the changing demands and pressures of the market, making sure the customer remains at the forefront of our decision making. In some cases that means improving our national and regional distribution centres and, in others, it’s about making sure we leverage our global leadership to bring the best product solutions to market as early as possible.
“The new distribution centre allows us to bring both of those workstreams together and will, ultimately, give our customers an even better service proposition well into the future.”
Q. Parts availability has been a hot topic – has AAG managed to stay on top of this task?
A. “With the level of supply chain disruption throughout the globe, this has been the hottest topic since 2020. We learnt a huge amount about being more agile in this area during COVID-19 and how to utilise our knowledge and resources to best ensure we have availability for the benefit of our customers. We significantly increased inventory levels throughout this period to ensure our customers could maximise their sales. We dedicated resources to managing this, and customer feedback has been overwhelmingly positive.”
Q. Finally, how would you sum-up the condition of the automotive aftermarket?
A. “The UK automotive aftermarket is in a great position. Car owners are very mindful of the current economic climate we all face, and the UK aftermarket is in a position to ensure that we can offer them a professional solution with world-class brands for their vehicle’s requirements. Obviously, with changing drivetrains, increasing levels of autonomous driving technology and issues around access to vehicle data, there are still challenges on the horizon.
“However, we recognise our responsibility to help the industry navigate through these challenges and shape them into opportunities. All that said, with the investment we’re making in our new distribution centre, it’s clear we have confidence the UK aftermarket will remain in great shape.”