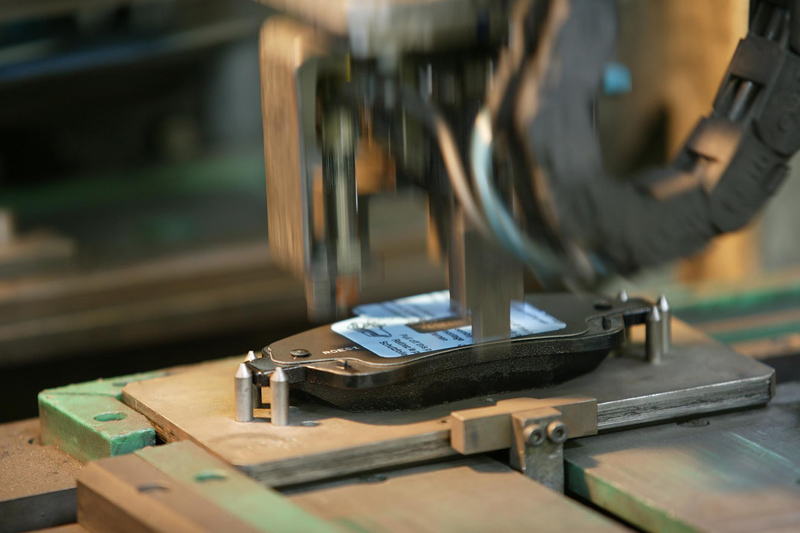
Scott Irwin, TMD Friction’s Head of Technical Training, fills PMF in on the company’s braking expertise.
Q. How has braking technology changed over the last few years and what are your future predictions?
Scott Irwin (SI): Over the past few years, we have seen advancements in lightweight technology, particularly for the brake disc. Keeping elements within the braking system as light as possible helps to improve fuel consumption, and is much kinder on the brakes. Looking a little further down the line, electromagnetic brakes could also feature more heavily in the future. This form of braking works on a slow or stop motion, using an electromagnetic force to apply mechanical resistance. When electricity is applied to the coil of an electromagnet, the magnetic flux attracts the armature to the face of the brake. As it does so, it squeezes the inner and outer friction discs together.
Currently, electromagnetic braking is not used on road vehicles, but has been implemented on trains and trams. With some adaptation, this technology could be used as a basis to improve a vehicle’s braking system, and may potentially lessen the environmental stresses currently caused by road vehicle braking.
Q. Are the demands of the aftermarket different to what they used to be?
SI: Yes, as technology used within cars becomes more advanced, braking products have needed to progress alongside it. This is evident even down to the type of brake grease that is applied to parts within the system. Although brake grease sounds like a small part of a brake replacement process, it has an important role, and the correct formulation is integral to how the system operates. For example, EPDM rubber is now a popular material used within the braking system, and if it comes into contact with mineral oil, the rubber will begin to swell. As a selection of popular lubricants are mineral based, this can cause a real issue for technicians. With this in mind, braking products need to be continually reviewed to ensure that they are in line with new materials and vehicle technology.
Q. In response to this, what has TMD Friction’s approach to R&D been?
SI: With regards to the R&D process, all pads start out life in our laboratory as raw materials. TMD Friction is continually evaluating new raw materials, often several hundred at any one time, in order to identify suitable ingredients for the development of new friction material formulations. These raw materials are converted into unique friction formulations, which are then rigorously tested to identify whether their characteristics make it suitable for inclusion within the TMD Friction material formulation portfolio.
Q. With regards to training, do you believe that motor factors should be provided with more opportunities to keep up to date with the latest developments in braking?
SI: We are committed to supporting motor factors across the UK, and we regularly host training sessions to help distributors understand more about Textar products. In turn, these sessions also help to support the technician network, as they can help to reduce the amount of returned stock due to incorrect fitment, thus improving the relationship between factors and garages.
Along with regular visits to motor factors, we also invite them to the factory so that they can see how brake pads are made first hand. This provides the opportunity for factors to see the process behind how brake pads are manufactured, and more specifically, how our approach creates truly unique products. Our factory produces 125,000 pads a week, which equates to around 12,000 per shift.