Why battery maintenance shouldn’t be left until winter
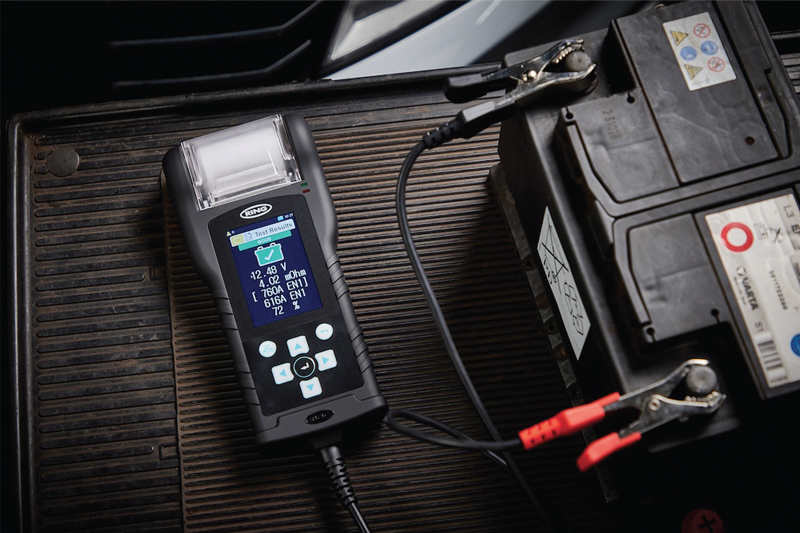
Ring Automotive believes that the health of batteries is not just a winter issue – but an all-year-round issue – so consistent checks are required. Its marketing director, Henry Bisson, explains the importance of battery maintenance.
It’s a well-known fact that hot weather can damage a vehicle battery just as much, if not more, than cold temperatures. The intense heat from the sun causes the vital fluids in a battery to evaporate, leading to weaker charges and accelerated corrosion. This damage from heat can linger for months, making the battery more likely to fail when the weather turns cold.
Motorists often overlook battery maintenance during warm weather because the battery seems to be working fine. Additionally, many people leave their vehicles unattended while on holiday, resulting in a battery that hasn’t been charged for weeks. Combined with the increased discharge rates due to heat, this can lead to premature battery failure, especially when the engine needs to crank in colder temperatures.
We recommend that technicians test every battery that comes into the workshop to determine if it needs replacing, charging, or if it will require a battery support unit during diagnostic work.
A battery that falls below approximately 12.5V is in ‘depletion’ mode, and damage to the internal plates can start to occur. Even if the battery isn’t completely discharged, unchecked damage can become permanent; however, a battery with a voltage around 12.5V can still be recharged and remain effective, so it’s crucial its charging status is monitored. We advise that technicians check all batteries on-site, including replacements, to ensure they are fully charged – ideally around 13.2V.
‘Win-win for supply chain’
For accurate battery diagnostics, our new battery analyser (RBAG950) is highly recommended. This tool provides a comprehensive health check of both 12V and 24V batteries and electrical systems in vehicles, including motorcycles, cars and vans. It tests various battery types, such as lead acid, AGM, EFB, gel, LiFePO4 lithium, and start-stop batteries.
The analyser features a graphical interface and can test the battery, alternator, starter and vehicle earth. Results can be printed with the built-in thermal printer, saved on an SD card or accessed via QR code.
Incorporating this battery testing presents a valuable revenue opportunity – up-and-down the supply chain! Also, promoting year-round battery testing can boost business and increase profit margins. It’s a win-win.