Understanding 5-wire wide-band oxygen sensors
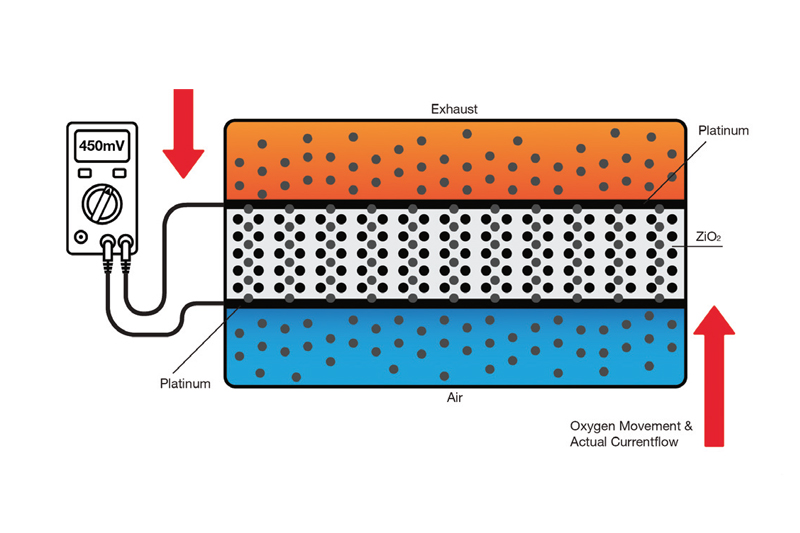
Precise engine control is paramount for optimising performance, emissions and fuel economy, according to bilstein group. A component that plays a key role in this balance is the 5-wire wide-band oxygen sensor – here’s Charles Figgins, technical marketing manager, to explain.
Found in modern diesel and direct-injection petrol engines, these sensors offer a range of benefits to ensure the ECU can accurately gauge fuel mixture and make real-time adjustments.
Let’s dive into the technology behind 5- wire wide-band oxygen sensors, their structure, operation and importance in engine management:
Unlike traditional narrow-band sensors, which measure only rich or lean conditions around the stoichiometric air-fuel ratio (14.7:1), wide-band sensors provide data across a broader air-fuel ratio range, from 8:1 to pure air. This range allows the ECU to make precise fuel and timing adjustments, resulting in better fuel economy, enhanced performance and reduced emissions.
How it works…
Both wide-band and narrow-band sensors share a core principle: the use of zirconium dioxide as a solid electrolyte that becomes conductive at high temperatures. In narrow-band sensors, a catalytic layer of platinum facilitates oxygen molecule dissociation, allowing oxygen ions to migrate through the zirconium dioxide when there’s a difference in oxygen levels between the exhaust and the air. This migration creates a potential difference, generating a voltage signal to the ECU.
Inside the sensor…
The 5-wire wide-band sensor consists of two Nernst cells, each with a distinct function:
• Measuring cell: This monitors oxygen levels between the reference air chamber and the exhaust gas sample.
• Pumping cell: This actively pumps oxygen in or out of the sample chamber to stabilise the oxygen level to a reference state.
By applying a specific voltage to the Nernst cell, oxygen is pumped through the zirconium dioxide, allowing for real-time adjustment based on the exhaust gas composition. The polarity of the applied voltage determines the direction of the oxygen flow, thereby allowing the ECU to precisely control the oxygen level in the sample chamber.
Operational process and maintaining stoichiometry
To maintain a stoichiometric air-fuel mixture (lambda 1), the wide-band sensor adjusts the oxygen level in its sample chamber so that the measured cell voltage remains stable at 450mV.
When the oxygen level in the exhaust rises, the black-yellow Nernst cell voltage drops, causing an imbalance in the op-amp circuitry. This prompts the pump circuit to drive current through the sensor, moving oxygen out of the sample chamber until stasis is restored. Conversely, when the mixture becomes rich and exhaust oxygen levels drop, the pump circuit moves oxygen into the sample chamber to maintain the stasis condition.
This balanced stasis condition, represented by a zero voltage output from op-amp B, allows the ECU to make realtime air-fuel adjustments based on exhaust conditions.
Importance of the heater circuit
The performance of a wide-band sensor is temperature-sensitive, requiring a steady operating temperature of around 760°C. To achieve this, the sensor relies on a heating circuit, powered by the vehicle’s battery voltage and controlled by the ECU through pulse width modulation. Temperature fluctuations affect the sensor’s resistance, so the ECU uses a diagnostic pulse to monitor resistance changes and adjust the heater circuit, maintaining optimal sensor performance.
Diagnosing sensor health
Faulty sensors can lead to inefficient combustion, resulting in higher fuel consumption and increased emissions. Regular diagnostic checks on wide-band sensors are essential for ensuring optimal performance and environmental compliance. A typical sign of a failing sensor is a disruption in the fuel mixture, often indicated by an increase in fuel consumption or unexpected emissions spikes.