TMD Friction provides best-practice winter braking tips
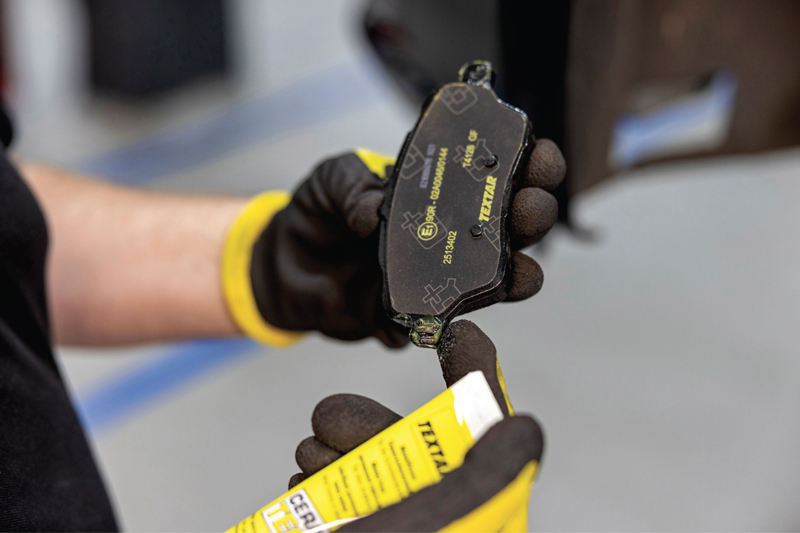
The car’s braking system consists of many components, most of them exposed, which makes them susceptible to all kinds of pollution, road grit and moisture – and in the winter, to slush and snow. Here, Scott Irwin MIMI, head of technical training at TMD Friction, explains the impact that winter conditions can have on the functioning of the braking system.
This applies to brake pipes and rubber hoses, calipers, ABS rings, as well as brake discs and pads. It is important, therefore, that you have access to the highest quality parts and the technical know-how on best-practice winter braking tips, to share with your customers.
Particular attention should be paid to brake pipes and hoses, both rigid and flexible. Under the influence of slush and snow, old brake fluid with a lot of moisture in the system can be a harmful influence on these parts, as they can start to corrode from inside or outside.
To verify a brake hose defect, you should encourage technicians to carefully examine the hoses and their metal terminals for leaks, rust or mechanical damage. The hoses need to be in good technical condition, as they act as the carrier of the brake fluid and are crucial for the proper functioning of the brake system.
The operational efficiency of the brake fluid itself can be checked using a special tester, such as TEX1000BFT from Textar, which allows the technician to determine the exact boiling point of the brake fluid.
Manufacturers recommend replacing it on average every two years or 60,000 km, whichever comes first. When replacing the brake fluid, we must remember that boiling point is not everything; for proper operation of all systems, such as ABS/ESP, it is not enough that the fluid does not ‘boil.’
It must have the right viscosity, which ensures sufficient fast pressure changes in the system. It is important to choose not only the DOT classification by number, but also the proper viscosity, such as DOT4 or DOT4LV.
ABS plugs and rings are vulnerable too
ABS plugs and rings are another element susceptible to adverse winter conditions. Some replacement plugs do not have factory seals, for example.
In this case, the most dangerous element is the moisture, which can cause corrosion of electrical connectors.
The problem of rust can also apply to calipers, brake pads and discs, which means in all places where moisture gets. The brake pads can corrode together with the guides, which will prevent their free movement during brake operation.
The winter period is conducive to these phenomena due to the increased humidity; for example, a characteristic rust coating may appear on the surface of the brake disc. If these are traces, when braking, the driver will hear the characteristic sound of scraping, similar to that of grinding steel with coarse sandpaper.
After a few braking operations, rust will come off and the specific noise will stop. In extreme cases, after a long standstill, corrosion can permanently damage the structure of the disc, so it is important that the technician can access high-quality parts and the owner is advised to drive the car regularly.
On the rear axle, the most common fault is the corrosion of the handbrake cables, which, if not used too often, tends to corrode faster. If the cable has a broken shield, water will get inside it. This causes contamination and progressive corrosion of the cable, especially of its ends, which in conditions of minus temperatures can lead to a blockage.
If the water in the cable shield freezes, it may not be possible to release the hand brake in the cold.
How to avoid winter problems
First of all, it is recommended to regularly check the brake system’s condition and if necessary to replace individual elements with new ones.
From the point of view of the correct operation of the brakes, assembly and maintenance of the system is very important.
It should be remembered that the appropriate points should be protected against corrosion with a dedicated ceramic or synthetic grease, depending on the purpose, such as Textar’s Ceratec. It is also worth using VM operating instructions.