How to help customers avoid alternator misdiagnosis
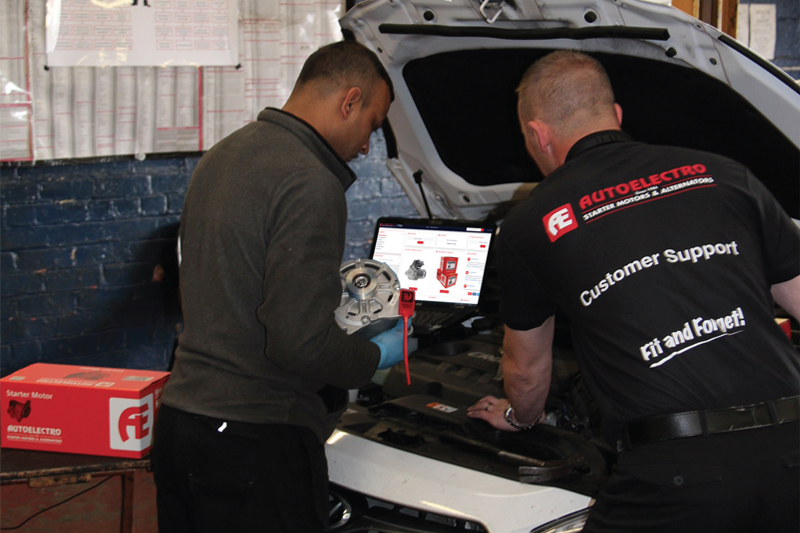
Remanufacturing specialist, Autoelectro, is advising its customers to remind workshops about the importance of checking vehicle software and ECU communication before diagnosing alternator faults.
With nearly four decades of industry expertise, Autoelectro is well-placed to highlight new trends, technologies, and challenges to the automotive aftermarket sector.
Modern vehicles increasingly rely on advanced communication between the alternator and the ECU to manage charging systems and warning lights. According to the rotating electrics remanufacturer, if a vehicle’s software is outdated, this communication may break down, leading to misdiagnosed faults. The alternator may be wrongly identified as faulty when the issue is actually with the vehicle’s software.
Autoelectro stocks over 5,000 part numbers, each tested to meet or exceed OE specification. Its team has discovered that newer alternators – especially those in Ford, Range Rover, and Audi models – can be prone to such issues if ECU-controlled systems or software updates are overlooked.
Autoelectro’s Harnek Bhogal said: “We’ve identified several part numbers, including some 48V MHEV systems, which require specific technical support available only through us in the aftermarket. Our recommendation for motor factors is to advise their customers to ensure that vehicle software is up to date before carrying out any diagnostic work. This simple step can prevent misdiagnoses and avoid unnecessary returns or replacements of functioning alternators.”
Building trust through quality and testing
One of the UK’s largest remanufacturers of starter motors and alternators, Autoelectro maintains complete control over its manufacturing processes. This allows the company to detect emerging industry trends and share valuable insights with the aftermarket sector.
Autoelectro’s ISO 9001 certification underlines this; the company claimed it is dedicated to exceptional product quality and stringent manufacturing standards, with the certification likely to enhance confidence that Autoelectro’s products meet the highest quality benchmarks.
Harnek continued: “Our ISO 9001 certification reflects our commitment to continual improvement and reliability. By maintaining these standards, we ensure our customers – both garages and motor factors – can rely on us for high-quality, dependable products. Furthermore, many of our units include OE components and are bench-tested on the latest OE test equipment to simulate real-world conditions.”
Comprehensive technical support available
Autoelectro is “determined” to support its customers and their customers with the right tools and resources. To help ensure correct diagnosis and installation, Autoelectro provides bespoke, part-specific technical notes included in the box with each unit. These technical notes are also available online through the Autoelectro 1986 Dashboard, an extensive online resource where users can access troubleshooting tips, common faults, technical advice and much more.
Harnek concluded: “It’s vital for motor factors to remind customers to review these technical notes before replacing any parts. Doing so prevents issues down the line, helps build trust, and, ultimately, ensures that the right diagnosis is made. Our comprehensive support system gives the supply chain peace of mind, knowing motor factors and workshops can rely on Autoelectro’s expertise.”