How OE-approved remanufacturers restore old parts
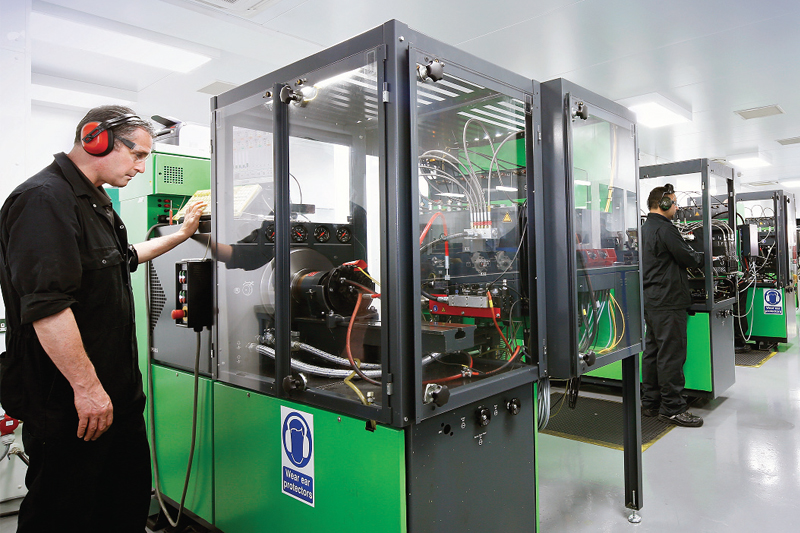
OE-approved remanufacturers restore old parts to like-new – or, according to Carwood, sometimes even better – condition, complete with a matching warranty. Here, the company explains its belief of quality parts not costing the earth.
According to leading industry associations, including The European Association of Automotive Suppliers (CLEPA), Motor & Equipment Remanufacturers Association (MERA), and Automotive Parts Remanufacturers Association (APRA), remanufacturing is defined as a “standardised industrial process by which cores are returned to same as new, or better, condition and performance. The process is in line with specific technical specifications, including engineering, quality and testing standards. The process yields fully warranted products”.
Carwood, with this definition at the forefront of its strategy and process, ensures that every single one of its parts – whether a fuel injector, starter motor, engine or turbocharger – and regardless of its destination – a VM, fleet or independent garage – goes through the exact same process.
Core inspection: Every unit is inspected against its acceptance criteria to assess its suitability for remanufacture. Carwood guarantees only good cores are used, because what is put in at the start has a bearing on what comes out at the end.
Disassembly: The units are then stripped down – any products with cracks, scrapes, faulty connectors, missing components, heavy corrosion etc are rejected and the material recycled. No gaskets or seals are reused.
Cleaning: All reusable parts are put through a rigorous multi-stage cleaning process to remove any unwanted particles and contaminants – this includes ultrasonic cleaning, hot water and sandblasting.
Reinspection: Carwood’s experts then inspect again, which includes the measurement and testing of individual components to ensure they are within OE tolerances.
Part replacement: All wearing parts – and any that are deemed unsuitable – are replaced with like-for-like OE parts.
Assembly: Carwood’s team then reassemble the units following OEapproved build specifications and processes. Its fuel pumps and injectors, for example, are assembled in an ISO certified, Class-7 clean room, capable of filtering down to 0.5 microns.
Test and calibration: All units are end-ofline tested using modern test equipment and test plans – Carwood insists no product will leave its factory until it has met OE performance standards, as a minimum. In the case of common rail injectors, a new calibration code or trim code is generated to improve the precision and timing of the injected fuel for optimum engine, fuel consumption and emissions performance. This code should be programmed into the ECU when the injector is installed in the vehicle.
Carwood believes that it is only through this “highly engineered, rigorous process” can it be confident that every remanufactured part has been returned to VM original factory specification. It is ensuring a product is just as good as new, sometimes better, with a warranty to match – whilst also being a positive for the environment.