How Nissens tackled tricky VAG diesel EGR valve
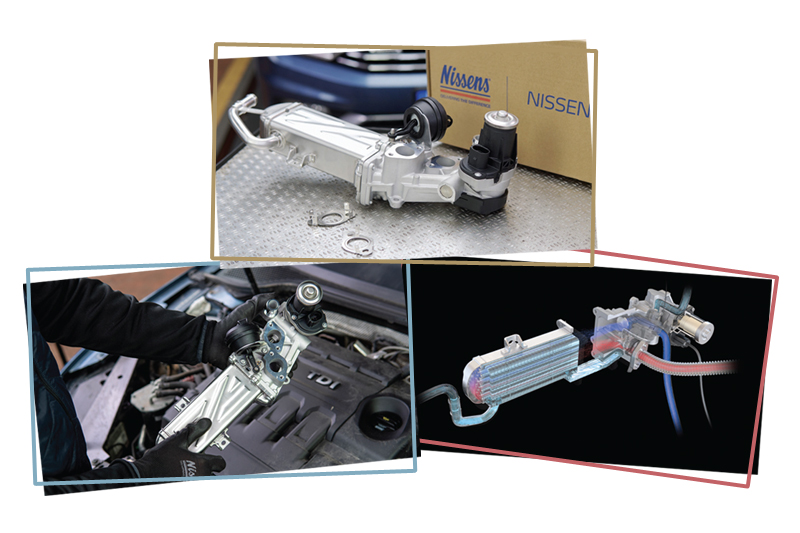
Nissens Automotive prides itself on a “proven track record” of identifying business development opportunities for both you and installers.
For workshops, this is demonstrated by a “high-quality, fit, and finish of each component”, along with a policy of including all necessary parts for first-time, high-standard performance. For the factor community, Nissens highlights opportunities related to linked applications and problematic references, and by introducing reengineered products that provide practical solutions.
Having previously drawn attention to the comparatively high failure rate of the exhaust gas recirculation (EGR) valve used in more than seven million European VAG diesel applications utilising the 1.4, 1.6 and 2.0L TDI units, Nissens is keen to update you and highlight the increased range of replacement products the company has added to address this ongoing problem.
To recap, the EGR valve in these applications can be particularly problematic, according to Nissens Marketing Manager, Jan Zieleskiewicz: “It is especially susceptible to heat and vibration, as well as excessive engine load. Naturally, the faulty valve has to be replaced, but as the issues are largely due to the design of the OE part, factors must be aware that these malfunctions can occur both in the original and replacement part, so opting to supply their workshop customers with a superior solution provides them with a great opportunity, particularly in light of the growing range of references that Nissens now offers.”
Nissens believes it has applied several design improvements over the original and proved that is the case over a series of comprehensive tests. Consequently, Nissens is confident its solution addresses the issues that contribute to the OE valve’s premature failure and ensures its proper function, while delivering performance standards as defined by the VM and doing so over a prolonged lifespan.
Optimised gearbox design: Recognising the problems associated with heat and lubrication, Nissens reduced tolerance and friction, by applying specific PTFE, high-temperature resistant grease, and upgraded the plastic material of the gear wheels in the two-stage gearbox.
Improved design of the valve stem: To avoid the known malfunction of the valve caused by the engine load and vibrations, Nissens is confident it has improved the valve’s stem and lever arm fixings by applying a unique design spiral pin.
DC-motor design upgrade: Nissens believes it has optimised the motor’s bearing system to ensure function in harsh working conditions, with vibrations and frequent temperature changes.
Although Nissens part number 98178 was the first EGR valve module to benefit from these modifications, superseding 10 OE part numbers in the process, the Nissens team has now turned its attention to several other references to address similar issues and added five further EGR valves.
This extended range now covers 37 OE part numbers for 40 plus popular VAG applications, including multiple Audi A1, A3, A5, A6, Q3/Q5 and TT variants, as well as numerous VW models. Consequently, you don’t have to hold as much stock as previously.
The complete Nissens EGR valve and module range now extends to 188 references that cater for 1,258 OE part numbers, which represents more than 60% of the vehicle parc. The closely related EGR cooler offering includes 86 references and 375 OE part numbers, almost 50% of the vehicle parc. Both product groups sit within the Nissens efficiency and emissions programme, which contains four product lines catering for almost 15,000 references and more than 8,000 OE part numbers.
In addition to providing replacement products, Nissens offers extensive support by directing your workshop customers to various technical resources. These help technicians diagnose underlying issues and correctly install the required replacement components: www.rdr.link/FAH023 and www.rdr.link/FAH024