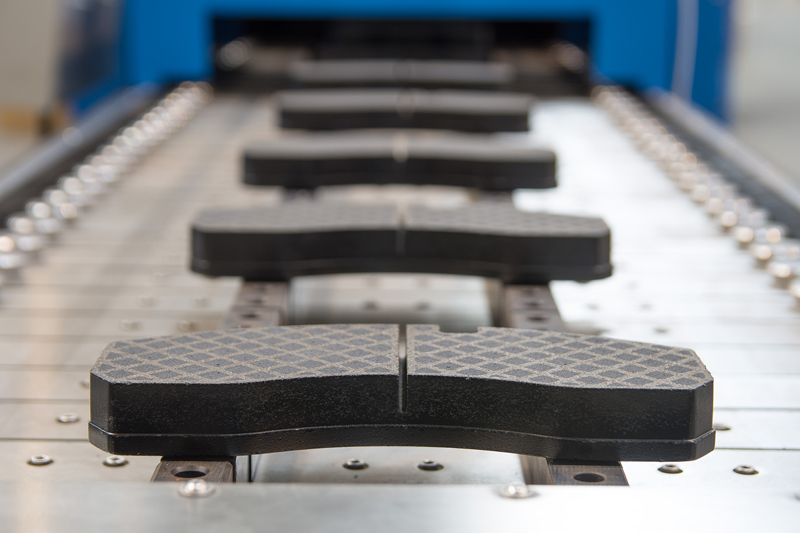
Lumag, the Polish manufacturer of friction materials, explains the science behind its recently launched Green Coat braking technology.
It is a commonly known fact that, following brake pad replacement, it is advised that braking is kept calm, considered and without any sudden manoeuvres for the first few kilometres. As we know, this expectation is rarely true, with heavy braking the mainstay for most drivers.
Until now, the only real saving grace for early brake pad usage is a phenomenon called the ‘Third Body Layer’ which helps improve brake efficiency.
Simply put, the term ‘Third Body Layer’ denotes a mixture of various substances and materials involved in the braking process. To use more technical terms, it is a layer of carbonised organic products, metal sulphides and oxides, and other non- reactive components of the friction material and of the brake raceway. It is formed during the breaking-in of brake pads and discs. Small particles of the friction material and brake disc are released during breaking-in, and in turn are captured by surface irregularities of both interacting components. The resulting mixture has a different composition than the original parts.
During braking, the Third Body Layer separates the friction material from the disc, protecting metallic components of the friction material from gluing together or fusing with the disc. This process involves a phenomenon called ‘adhesion’ or ‘micro welding’. As long as the Third Body Layer exists, the friction coefficient remains stable, which directly translates into braking efficiency and, consequently, improved safety.
But what if we could counter the importance of the Third Body Layer by creating an additional valuable layer that is added to the brake pads during the production process? With its new Green Coat technology, Lumag has done just that, and in doing so, is setting new standards in braking safety and quality.
Representative of a £145,000 investment at its Budzyń factory in Poland, Green Coat from Lumag offers even greater braking safety from day one, with braking distances from 50 to 0kph (during breaking-in of newly installed pads) reduced by up to three metres.
Talking about Green Coat, Lumag UK’s MD, Colin Smit, said, “Despite the EU requirement, ECE R90, which defines the maximum allowed braking distance, very few brake pads really achieve full braking efficiency until they have covered in excess of 200 to 300km. More commonly known as ‘green fade’, this drop in braking force is caused by excessively violent pressing down on the brake pedal, when brake pads have not been broken-in yet. The Third Body Layer has a huge part to play in reducing this timescale but can only really be achieved if – and it’s a big if – brakes are used efficiently and lightly. This is a rare occurrence as normal driving styles take precedent over safety and the breaking-in process of brake pads. Green Coat, however, works to reduce this concern.”
Lumag’s Green Coat is a thin layer of silicates that is applied directly to the outer friction surface of the brake pad during the production process. Brake pads featuring a layer of the Green Coat provide a higher coefficient of friction right from the first application of the brakes, which significantly shortens the braking distance during the bedding in process. The layer lasts for a few dozen brake applications, which overlaps with the time a new brake needs to reach full efficiency, or for the Third Body Layer to fully form.
Colin concluded, “Tests indicate that the Green Coat can shorten the braking distance from 50 to 0kph by up to three metres. When you consider that drivers trust their brakes to safely stop their one tonne plus vehicle, then every little bit of distance saved can make a life changing difference.”
New line for Green Coat
As a part of the investment project, Lumag’s factory, located in Budzyń in the Wielkopolska region of Poland, will be extended by a stand-alone line used for the application of the Green Coat. The semi-fluid material will be screen printed on the working surface of the friction material, while a laser screen positioning system will ensure the right position of the grid pattern developed by Lumag’s experts. Next, brake pads will be automatically conveyed to a drying module. It is especially worth noting that no solvents are used in the production process, which makes it environmentally friendly.