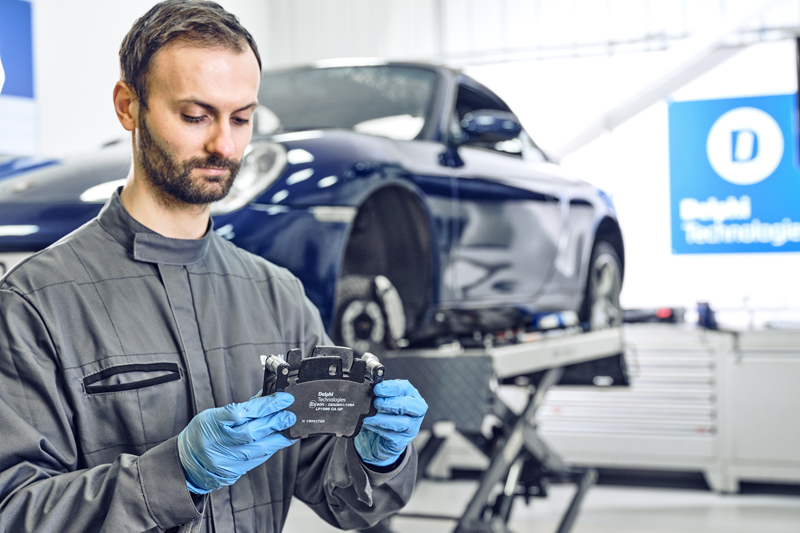
As was promised in the November/December 2020 issue, here is the full interview with Philip Mitchell and Julian Goulding, UK Technical Services Manager and Marketing Manager North Europe at Delphi Technologies, respectively, regarding the company’s training offering and its ‘first-to-market’ braking components.
Q: It’s great to hear about the resumption of the company’s training offering. How long had it been paused for, and why did it stop in the first place?
Philip Mitchell (PM): It had been paused since March. We could see issues with COVID-19 on the horizon and took the decision to stop training courses a week before lockdown. The decision to stop was taken to protect employees and delegates, who are, of course, our number one priority.
With extensive measures put in place to protect course leaders and students, training was restarted in September. To ensure optimum safety for everyone on-site, extensive PPE is provided, social distancing is adhered to, and the temperature of everybody entering the building is taken.
Q: What is the basis behind Delphi’s training programme? Why has it sought to offer independent technicians such training?
PM: There is a massive shortage of skilled people across the sector, and this skills shortfall will lead to greater challenges if the problem is not addressed. Current training trends are for traditional maintenance items, but people are wary that they can fall behind without focusing on developing skills to meet the challenges posed by emerging technologies, such as hybrid powertrain.
For a long time, there has been a big training hole in the industry outside of college or main dealer courses, which our modules aim to address. People want to see a training route for their career, and visibility of such a structured, in-depth offering is a confidence booster for newly qualified professionals or employers knowing that they can adapt to future technologies.
We are fortunate in that, as an OE tier one supplier, we are able to use this expertise to also help prevent warranty returns. By this, we mean to upskill staff and stop warranty returns through human error resulting in incorrect component installation or misdiagnosis.
Q: Are the training sessions virtual, or can they take place on-site?
PM: All sessions took place on-site before COVID-19, but the pandemic has forced all companies to adapt their established practices. We are currently running an online trial with a half-day webinar practical, and are set to imminently launch our new e-learning platform. It is very rare to find an OE supplier that provides such an offering alongside practical training on-site. The programme offers a unique blend of lecturing, simulation and practical learning opportunities.
The Delphi Technologies technical hotline helps to mould some of the content by providing feedback on the questions and concerns being raised by customers on the hotline. This can then be incorporated into the syllabus, if it’s not already covered. Further ideas are also fed back from the workshop, ensuring that when crafting the modules, we are drawing on our entire OE expertise and aftermarket experience.
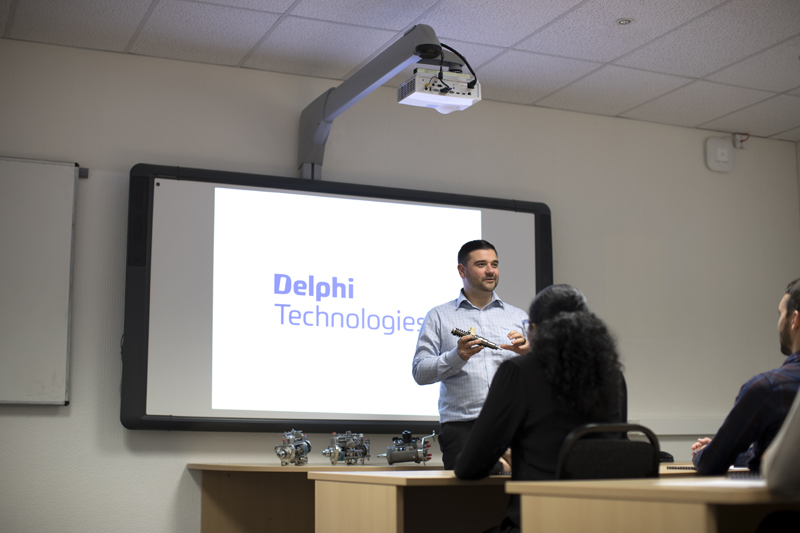
Q: Who constructs and leads these sessions?
PM: Everything is done in-house by our five-strong, dedicated training team, the members of which boast a combined experience of 90 years. IMI courses provide the criteria of what needs to be covered, and we draw on our own research and experiences to structure our courses.
Q: Are courses entirely practical, or do they contain a theoretical segment, too?
PM: Our research and feedback suggested that delegates wanted an increased level of practical challenges, which we have worked to incorporate into the latest syllabus. For example, 70% of the new ADAS course is practical. A more common split is for a 50/50 or a 60/40 balance in favour of practical.
We have seen some people opting for e-learning as a way to brush up on their skills, but delegates do like to be hands-on. Additionally, we’re seeing more and more colleges and organisations, such as police forces, wanting us to come to them for convenience. We can accommodate that, and before COVID-19, it was something we were pushing forwards with. Obviously, that has been disrupted, but delivering training at a client’s premises is something we will continue to pursue when it is safe to do so. Some courses lend themselves well to it, and when you think that some clients may be sending upwards of 10-20 delegates to us for training and covering their expenses for travel and accommodation, it’s very cost-effective for them to have us visit them instead.
Q: How many different courses are there for prospective trainees to get stuck into?
PM: There are a total of 26 courses. These are broken down into four different levels: fast fit; service; diagnostic; and master technician.
We tend to expand the offering by one course a year, but a huge amount of time is committed to refining existing courses to ensure that they remain current and relevant. Perhaps unsurprisingly, the most popular course is Hybrid Level 3 IMI, which covers everything other than working on a live battery. We have gradually grown into hybrid and ADAS training as the technology has been introduced.
One trend we’re seeing is that people want to do a suite of courses with a dedicated path of training, rather than picking a single course from the catalogue.
Future additions to the course could focus on Borg Warner products, as the company is able to offer vast expertise in technology areas, such as turbocharging, where Delphi Technologies doesn’t have a presence.
Q: Does the approach taken to these training courses differ throughout the year, perhaps as certain components become more relevant?
PM: No, we have structured the training to ensure that the courses remain relevant all year round.
Q: What would you say makes Delphi’s training programme stand out for those in the independent aftermarket?
Q: Delphi’s programme is structured and targeted, offering a career path progression of five to six years. It also offers the opportunity to be trained by a manufacturer of OE components and have these parts as a resource on site.
We have a highly experienced training team, some of whom are ex-OEM, and, with the availability of e-learning, we operate a flexible learning platform that is suitable for a range of delegates. Situated in Warwick, our training centre is also ideally placed to serve the entire country, but where distance is an issue, we can now offer enhanced e-learning opportunities.
It’s good for both delegates and their employers, providing the employee with the skills to do a job competently and efficiently, while also helping the business retain that person by showing them there is a genuine way for them to progress.
Q: Does Delphi offer any training for motor factor employees? If not, are there plans to?
PM: Absolutely! The existing courses are ideal for factor employees – the programme can be accessed by anybody and can benefit anyone in the motor repair or aftermarket industry.
There’s something for everyone at every level, from specialist repair courses for truck injectors to fast-fit, tyres and brakes, as well as high-end hybrid and ADAS technology. We’re here to teach anybody that wants to learn.
Q: Switching the focus to some other Delphi Technologies news, please tell our readers all about the company’s efforts to be ‘first-to-market’ with a variety of brake pads.
Julian Goulding (JG): Being an OE supplier provides Delphi Technologies with insight into upcoming aftermarket trends and requirements. This enables us to be first-to-market for a wide range of aftermarket brake pads, including, most recently, new Land Rover models, the Mk8 Golf and 2020 Honda Jazz. The main benefit is that it enables factors and garages to remain stocked for the latest versions of the most popular models. Stockists will have an immediate competitive advantage over rival businesses that do not stock Delphi components and will therefore have delays when servicing the latest models.
However, the accelerated speed to market does not compromise Delphi’s quality; our brake pads feature 100% in-house friction manufacturing that has been rigorously tested against competition materials. We offer over 99% brake pad coverage of all vehicle manufacturers in the EU.
Q: Why did such an effort go towards brake pads in particular?
JG: As a consumable with a wear rate that can be influenced by driver style and vehicle use, brake pads are one of the first critical items that normally need to be replaced on a new car. For example, higher mileage vehicles and light commercial vehicles can require brake pad replacement after as little as six months.
Q: Has the company ever achieved this before?
JG: The commitment to achieving first-to-market has always been there, and we have a solid track record for achieving it. It’s something we’re very proud of. What has been a huge help in allowing us to do this is significant investment in catalogue information for cars in operation, which enables us to see the volumes that will be forthcoming.
The proliferation of new car models and the rate of new launches has placed increased pressure on the aftermarket to meet demand, but as an OE supplier, we are able to see vehicles that are coming to market in advance and prepare for their arrival. We also have the data to link existing parts to new vehicles, which provides a crucial time advantage and can simplify aftermarket parts supply.
Q: What is the exact process of being ‘first-to-market’?
JG: In short, reverse engineering of the OE pad. Delphi Technologies offers no compromise on testing, development or analysis, and our offering matches the OE part 100% in terms of quality, performance and durability. Of course, all fitting accessories are also thoroughly researched and developed before supply, ensuring that the pads can be efficiently and correctly installed.
Q: Are there any plans to expand this ‘first-to-market’ network?
JG: In three months alone, 12 first-to-market vehicle applications have launched. This is a key focus area for Delphi Technologies, which the company remains committed to. It is a crucial element of our business and provides valuable support to customers that look after large fleets in particular.
Q: Will these brake pads be immediately available to motor factors?
JG: Absolutely! As soon as they’re announced, they’re available to purchase.