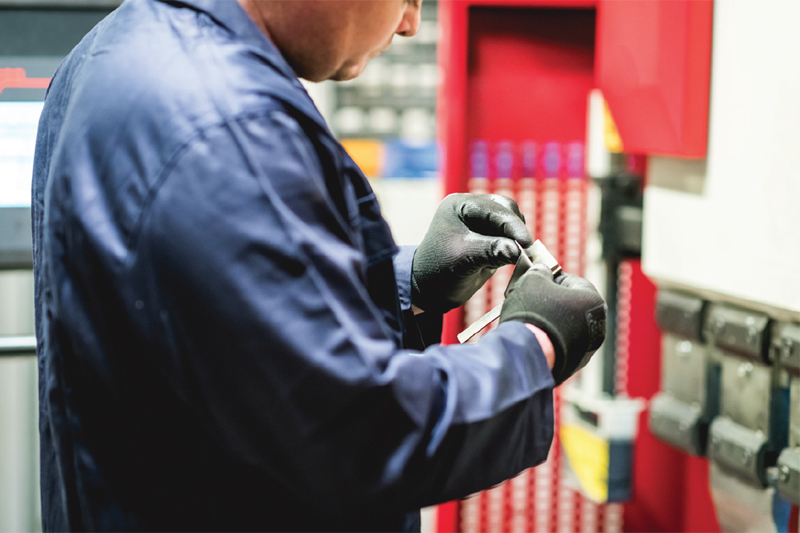
BM Catalysts’ Commercial Director, Mark Blinston, discusses the R&D steps taken by the company to ensure its products are in line with emissions regulations.
As with many other industries, the growing pressure from the UK Government and global legislators on consumers to reduce their carbon footprint has naturally forced the automotive aftermarket to react sooner rather than later to meet the rising pressure and provide motorists with an efficient solution.
Although zero-emission alternatives are available, new car sales fell by 40% in January 2021 in comparison to January 2020 as a direct result of the ongoing pandemic.
Most EV registrations in 2020 were for company cars, indicating that private buyers need stronger incentives to make the switch, as well as more investment in charging infrastructure, especially public on-street charging.
There is no denying that there is a clear shift in the direction of travel towards cleaner fuelled vehicles, but on the ground, more drivers are now holding on to internal combustion engine (ICE) vehicles for longer periods of time, and this presents an opportunity to forward-thinking aftermarket companies.
The UK aftermarket has specialist knowledge, experience and expertise in abundance, and is no stranger to adapting quickly to meet ever-changing demand and a diverse vehicle parc. As a sector that has often had to be proactive to thrive and survive, there is a prosperous future ahead for the automotive aftermarket. This is particularly true for companies with effective R&D procedures in place that enable them to make products that can effectively control emissions, and that motor factors can have confidence in stocking.
Identifying market trends
By investing in an extensive product development programme, companies are able to keep a close watch on market trends and identify future popular parts before the market demands them.
This enables them to be proactive and always remain one step ahead, as they can forecast product surges and ensure they have the appropriate levels of stock necessary to meet demand, without affecting delivery times.
As well as regularly introduced new-torange parts to expand vehicle parc coverage, BM Catalysts also carries out ongoing R&D work to identify additional fitments, offering greater choice to motor factors.
Testing
With two hi-tech manufacturing facilities and an additional warehousing site covering a total of 163,000 square feet, BM Catalysts is committed to an extensive testing programme that enables the company to bring innovative product developments and precision engineering to the aftermarket. This includes significantly testing the parts on vehicles before they are submitted for homologation.
BM Catalysts’ range of homologated cats and DPFs are tested in accordance with relevant emissions standards for vehicles the product is designed to fit and in accordance with Regulation 103R, ensuring confidence in their performance in comparison with an OE product.
Embracing new technology
As well as using the best materials possible, we use advanced techniques to ensure everything from sub-components to finished products are designed to the highest possible quality and fit.
Continual investment in the latest high-tech machinery ensures the company remains at the forefront of development and new technologies. It also means that 90% of the components used in finished products are manufactured in-house to ensure total control over quality. For example, our lambda sensor ports are 14% thicker than those of other suppliers in order to reduce the defect rate during the welding process.
It also uses CNC milling to refine its processes, with the technology allowing quick and easy production of large batches of flanges, as well as guaranteeing accurate repeatability.
BM Catalysts parts are patterned from OE, including the use of innovative technology, such as laser mapping, to replicate OE standard fit. Parts are also manufactured from 409 grade stainless steel, which is preferred by OE manufacturers due to its strength and resistance to corrosion.
What’s more, its 1D tube benders create extremely tight bends in the pipe work, which is essential for the manufacture of tubular maniverters.
Educational insight
With demand constantly changing, ongoing education and insight is key, and it is therefore important to offer support and continually listen to partners and the wider aftermarket.
By working collaboratively with customers and offering technical support where necessary, such as fitting kits, helplines and online videos, BM Catalysts is able to identify trends and potential issues, and adapt accordingly.
We have dedicated product development analysts who constantly monitor vehicle figures in global markets, along with automotive design, technology and construction to ensure the research and development department is well ahead of the game.