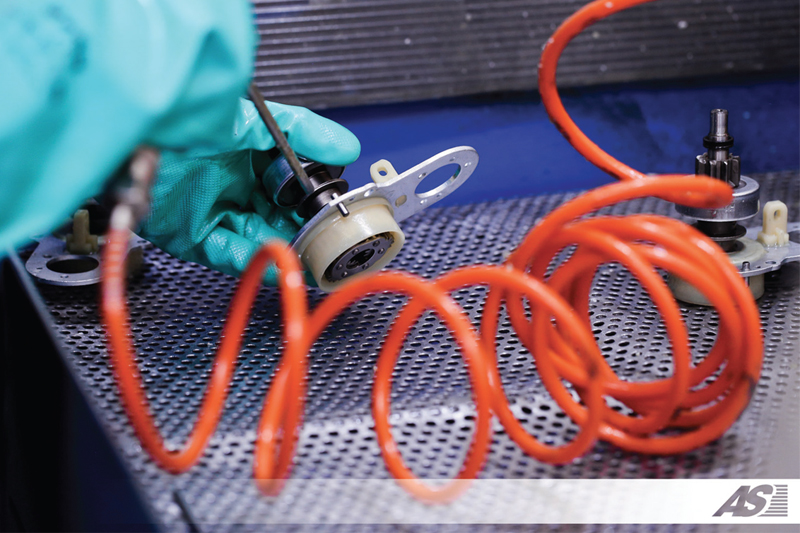
Based in Gdańsk, Poland, AS-PL supplies parts and electrical components. Established in 1992, it employs more than 300 professionals and works alongside distributors and wholesalers in around 100 countries – intrigued? Here’s more!
The company’s mission is to “provide top-quality goods tailored to market expectations while using state-of-the-art technologies”. AS-PL’s core products are alternators, starters, and components. In 2004, products manufactured under the brand name AS were introduced. Currently, the company offers more than 24,000 different products with a total of almost 610,000 reference numbers in order to provide its customers with a wide selection of original products and their replacements
The AS-PL products are divided into three product lines:
- Premium Line: the option addressed to customers who are looking for the best quality. Products supplied by OEMs and selected products of AS brand
- Standard Line: the leading product line of the AS brand, an option directed to customers looking for high-quality and reliable products at competitive prices
- Economy Line: a line of products that merge quality at a reasonable price at “favourable prices”.
In 2016 a production plant in Lubichowo, Poland was opened. It houses production lines with innovative solutions and specialist machinery supplied by Canadian D&V Electronics, a warehouse, and administrative space. The facility contains testing machines for controlling and improving the quality of AS-PL’s products and positions for the process of remanufacturing.
AS-PL has three branches abroad: in 2017 AS-PL UK Ltd. was opened in the UK. In Italian Moncalieri, the next office and warehouse (AS- PL ITALIA S.R.L.) is located and operating since 2019. Spanish Valencia houses AS-PL ELECTRICOS ROTATIVOS S.L. that was opened in 2022.
Additionally, the UK branch is set to be expanded with a warehouse and office area of space of 1000m2.
Remanufacturing sales continue to rise
For AS-PL, ecology is critical. The company claimed its remanufacturing process of alternators and starters takes place in a production plant using “advanced devices, in accordance with high-quality norms and assembly standards for assembling devices using new parts”. The process is carried out to minimise its negative impact on the environment.
AS-PL reported that customers’ interest in remanufactured products is not weakening – on the contrary! In the last few years, sales of remanufactured components have jumped (approximately 53%).
It believes this situation is affected by raging inflation and rising prices or difficulties in the availability of raw materials in the automotive industry. The policy of the European Union has had an influence too. This makes remanufactured products a very popular and cost-effective alternative to buying new parts.
AS-PL records the increase in remanufactured product sales every year. As a result, the range of models of regenerated alternators, starters, and parts has been expanding every year. The possibilities of assembling these products in the company’s production plant are also increasing and, currently, it is producing approximately 15,000 units per month. In addition, the return of cores for remanufacturing is not required.
From an environmental point of view, a customer that buys remanufactured parts reduces waste. In addition, it also reduces the consumption of valuable mineral resources and media, which are needed less to remanufacture the product than to produce a new part. This point of view is in line with the assumptions of the Green Deal policy and the circular economy. From an economic point of view, a remanufactured product is a cost-effective alternative to purchasing a new product. Each AS-PL remanufactured product has a two-year warranty.
Taking the remanufacturing process, from a technical point of view, into consideration, worn-out elements are replaced and working parts undergo tests. The process minimises the quantity of product waste and saves precious raw materials and utilities.
Damaged enclosures, bearings, and controller electronics are replaced with new ones.
Each product is accompanied with a completed final test report, which demonstrates that the product is in good working order and is reliable. It is inserted into a box together with the product, which then goes to a warehouse shelf where it waits to be delivered to the distributor network.
As a result of remanufacturing carried out in a professional manner, AS-PL stated that a product’s properties match its OEM equivalent.
Range expands with NOx sensors
The sensors are important elements of the selective catalytic reduction (SCR) system. The typical sensor consists of a measuring probe with an electrochemical sensor – it consists of two measuring chambers – a cable connecting the probe to the control module, a probe data processing module and a socket connecting the sensor to the ECU computer.
NOx sensors are located in the exhaust system; the input and output of the SCR system allows for continuous measurement of the concentration of harmful substances. The first sensor receives a measurement sample of exhaust gas, which has already undergone a treatment process in the DOC/DPF system. At the output, the NOx sensor is designed to monitor the performance of the SCR catalyst, which should reduce the volume of poisonous compounds to a certain level. Based on both measurements, the required amount of urea (AdBlue) injection is calculated to reduce the harmful substances as much as possible.