Dispelling myths surrounding polyurethane bushes
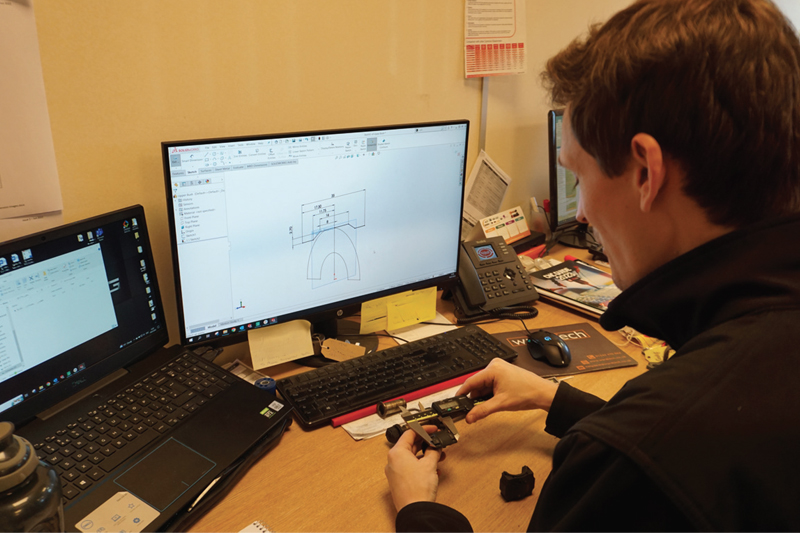
Strength, cost, lubrication and questions surrounding availability: Polybush Marketing Co-Ordinator, Ellis Blackman, tackles some of the burning questions surrounding polyurethane bushes and offers solutions in the process.
“Polybushes are too hard”
One of the biggest myths of polyurethane bushes is that they’re too hard and uncomfortable. This is a common misconception in the automotive arena. Contrary to this notion, the hardness of a polyurethane bush is a carefully considered aspect, in respect of design and manufacturing.
Before one is even created, extensive testing is conducted on both the mechanical properties of the suspension system it will be used in and the bush itself. This includes evaluating factors, such as hardness, to ensure that the final product not only meets but often exceeds the performance of the OE part.
One of the unique characteristics of polyurethane is its versatility in terms of hardness. This material can be formulated to cover a wide range of hardness levels, offering tailored solutions for various driving applications.
During the manufacturing process, the hardness of a polyurethane bush can be precisely controlled to suit specific needs. For instance, our firmest grade of polyurethane provides drivers with pinpoint steering response and a consistently stable ride across all speeds, making it ideal for high-performance driving scenarios, like track days or towing heavy loads.
Conversely, our softer formulations prioritise durability and shock absorption, ensuring a smoother and more forgiving ride over rough terrain or during everyday commuting.
Whether a driver is chasing precision on the racetrack or seeking comfort on the open road, there’s a polyurethane hardness option available.
“Polyurethane bushings are too expensive”
The misconception that polyurethane bushings are too expensive fails to consider the long-term cost-effectiveness of these durable components.
Polyurethane bushings boast impressive resistance to water, grease, ozone, and road damage, surpassing the lifespan of traditional rubber counterparts by a significant margin.
Often dubbed as ‘fit and forget’ products, they offer exceptional longevity, maintaining their performance without degradation over time. Unlike rubber equivalents, polyurethane bushings do not require frequent replacement, making them a wise investment in the long run.
We deal with the likes of West Midlands Ambulance, where premature bush wear was causing headaches for its fleet. With rubber bushes unavailable for separate purchase, the solution had been costly full replacements of anti-roll bars and leaf springs at regular intervals. However, upon realising the potential for cost savings, a switch to Polybush was made.
This decision resulted in a substantial £700 reduction in parts costs per vehicle, illustrating the significant financial benefits of investing in polyurethane bushings.
In essence, while the initial cost of polyurethane bushings may seem higher, their extended lifespan and reduced need for replacement make them a smart and cost-saving choice for vehicle owners and fleet managers alike.
“Grease is required to fit a Polybush”
Applying grease is not necessary when fitting our polyurethane bushes; in fact, it’s strongly discouraged! Our bushes are meticulously designed with an interference fit, precisely engineered to specifications.
While grease might seem like a logical choice for lubrication, its use can lead to unintended consequences. When grease is applied, the bush tends to rotate within its housing, effectively transforming it into a makeshift bearing. This rotation not only causes potential squeaking noises but also creates a situation where the grease remains trapped between the bush’s outer surface and the metal of the arm. Over time, this trapped grease can act as an abrasive, causing premature wear and damage.
Instead, we recommend using alternatives, such as tyre soap or washing up liquid, during the installation process. These substances provide sufficient lubrication to ease the fitting process while also drying quickly, effectively eliminating any residual movement within the housing.
By following this guidance, your trade customers will be able to complete a smooth and hassle-free installation of our polyurethane bushes, without the risk of long-term complications associated with grease application.
“Can you make custom bushes? I’ve built my own car”
At Polybush, we understand the unique needs of custom vehicle enthusiasts. That’s why we offer a comprehensive ‘Can’t Find What You’re Looking For’ section on our website specially curated to cater to a diverse range of vehicles and applications.
In this section, there is an extensive selection of polyurethane bushes, meticulously engineered to fit a variety of vehicles, from classic models to the latest performance beasts. Whether tackling a restoration project or fine-tuning a bespoke build, our range of bushes covers a wide spectrum of sizes and types to suit specific requirements.
From control arm bushes and subframe bushes to differential mounts, our catalogue boasts an array of options designed to enhance the performance, durability, and precision of a vehicle’s suspension system. Each bush is crafted with precision and expertise, ensuring a perfect fit and long-lasting performance, even under the most demanding driving conditions.
“Do you just make stuff for cars?”
At Polybush, our expertise goes beyond suspension bushes. We’re proud to offer our polyurethane moulding services for a diverse range of commercial projects, catering to various industries and applications. Whether it’s bespoke fence post moulds, specialised cricket stump holders, or even military-grade components, Polybush can help.
Our manufacturing facilities and experienced team enable us to tackle projects of all sizes and complexities with precision and efficiency. We understand that each project comes with its own unique requirements and challenges, which is why we offer personalised solutions.
From concept design to final production, we work closely with our clients every step of the way to ensure that the end-result exceeds expectations. Whether you require a small batch of custom components or a large-scale production run, Polybush has the capabilities and resources to deliver on time and within budget. Our commitment to quality and innovation is reflected in every project we undertake. Utilising the latest technologies and materials, we produce durable, high-performance solutions that stand the test of time.